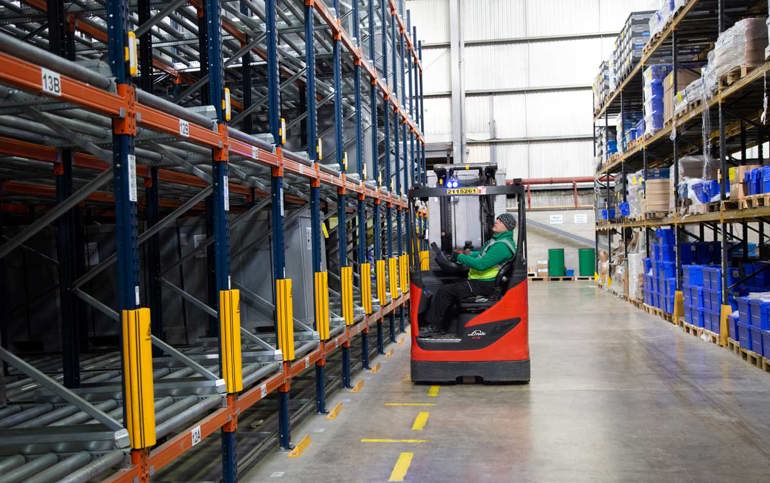
Management guru Peter Drucker once said: "The best way to predict the future is to create it." As technology and warehouse efficiency converge, these words have never been more relevant.
The weight on the warehouse safety manager has become increasingly onerous. The pressure to meet ever-tightening deadlines, handle unpredictable demand spikes, and maximise every square metre of space is relentless.
E-commerce booms, Black Friday frenzies, and holiday season rushes have turned peak seasons into a high-stakes obstacle course. So, how do you keep goods flowing at lightning speed while minimising errors and downtime? It's like trying to conduct a symphony orchestra while the stage is moving. And here's the bottom line - as you're pushing for peak efficiency, you can't afford to let safety standards slip.
The mainstream media is quick to shine a spotlight on workplace incidents, especially during those high-pressure periods. The old ways of balancing productivity and safety just aren't cutting it anymore.
As someone who's been developing solutions for these exact challenges, I've seen firsthand how the right technology can transform operations, boosting efficiency and enhancing safety in one fell swoop.
Old habits die hard - the cost of outdated systems
For many years, warehouses have relied on manual processes and reactive approaches to manage their operations and racking systems. This approach comes with hefty hidden costs. Inefficiencies that go unnoticed can snowball into major operational issues, leading to missed deadlines, dissatisfied customers, and a hit to your bottom line.
In addition, the old way of doing things eats up time and is prone to errors. Manual inventory checks, paper-based systems, and reactive maintenance schedules are like trying to build a skyscraper with a hammer and nails. It might get the job done eventually, but at what cost? This inefficiency not only impacts productivity but also increases the risk of accidents.
Knowledge is power - A data-driven revolution
Welcome to Industry 4.0, where Internet of Things (IoT) sensors, wearables, and clever data crunching are turning warehouse management on its head. These technologies offer real-time monitoring and insights that we couldn't have imagined a decade ago, pioneering a new approach to efficiency and productivity - every rack, every forklift, every square inch can now be monitored, analysed, and optimised.
Picture a system where every movement in your warehouse is tracked, every piece of equipment is monitored, and every process is optimised in real-time. It's not science fiction - it's happening now in warehouses with cutting-edge IoT solutions.
These systems use sensors and advanced analytics to keep a constant eye on your operation. When a bottleneck forms or a storage unit needs maintenance, the system flags it immediately, allowing you to address issues before they impact your efficiency.
This real-time information means inefficiencies can be nipped in the bud before they become big problems, saving time, money, and yes, even improving safety along the way.
It's problem-solving at its finest, powered by digital transformation.
From gut feeling to gold dust - making data actionable
But the real magic of these Industry 4.0 solutions isn't just in gathering data - it's in making sense of it. Advanced analysis platforms can take information from sensors across the whole facility and turn it into insights you can leverage.
These insights go way beyond simple performance reports. They can show patterns in warehouse traffic, evaluate risk, and even predict potential bottlenecks based on historical data. This level of analysis lets warehouse managers make smart decisions about optimising layouts, training staff, making upgrades to improve efficiency. And the best part? Enhanced safety naturally follows these efficiency improvements.
Predictive prowess - optimising before issues arise
One of the most exciting uses of these technologies is in predictive maintenance and optimisation. By analysing patterns in equipment usage, inventory movements, and operational flow, these systems can forecast when and where you might face challenges. This approach lets warehouses plan ahead, optimising processes and scheduling maintenance at the most convenient times.
The benefits are massive. Not only does this reduce unexpected downtime and boost overall efficiency, but it also creates a safer working environment. No more mad rushes to meet deadlines because of sudden equipment failures or process bottlenecks. It's a pioneering approach to warehouse management, turning your team from firefighters into efficiency experts.
Efficiency meets safety - a culture of continuous improvement
Beyond the operational benefits, these Industry 4.0 solutions are creating a culture of continuous improvement. By providing clear, objective data on all aspects of warehouse operations, they're encouraging a more proactive and engaged workforce.
Case studies of warehouses where these systems have been implemented have shown a notable shift in how employees approach their work. They become more aware of efficiency and naturally more careful in their operations, leading to fewer errors and accidents.
Award-winning innovation
We've always been at the forefront of warehouse innovation. That's why we developed our award-winning solutions, RackEye™️ and CONEK™️, to address the very challenges I've been discussing. These products are at the heart of our disruptive, problem-solving approach.
RackEye™️, our smart sensor technology, is a prime example of Industry 4.0 in action. It keeps a constant eye on racking structures, monitoring their health and usage patterns. This system allows for optimal use of storage space and early detection of potential issues, maximising efficiency and preventing costly downtime.
Working alongside RackEye™️ is CONEK™️, our cutting-edge data platform. CONEK™️ takes all the info RackEye™️ gathers and turns it into actionable insights for warehouse managers. It's not just about collecting data - it's about making that data work for you, helping you to make smarter decisions to optimise your operations. This is Industry 4.0 at its best, driving efficiency improvements across the board with enhanced safety as a welcome bonus.
We are proud that RackEye™️ and CONEK™️ have been recognised with industry awards. But what really matters to us is how these solutions are already helping warehouses around the world streamline operations, boost efficiency, and yes, improve safety too.
They are proof that the future of warehouse management isn't just a pipe dream - it's here, and it's making a real difference in businesses like yours.
Tomorrow's warehouse, today
Looking ahead, the potential uses of these technologies are mind-blowing. AI-driven platforms could analyse multiple data points to optimise warehouse layouts, predict seasonal demand changes, or even automatically adjust storage strategies based on changing inventory.
We also see promising developments in linking these management systems with other warehouse tech, like inventory systems and automated guided vehicles. The result is a joined-up, data-driven approach to warehouse management that promises to revolutionise the industry.
Embracing change
The challenges facing warehouse operations are big, but so are the opportunities presented by Industry 4.0 technology.
IoT sensors, real-time monitoring, and advanced analytics aren't just buzzwords - they're powerful tools already transforming how leading warehouses operate.
We can stick to our old ways and struggle with their limitations, or we can embrace these new technologies and the benefits they bring. For me, the choice is clear. By adopting Industry 4.0 solutions, we can create more efficient, productive (and safer) warehouses that are ready to tackle the challenges of today and tomorrow.
The future of warehouse management is here, driven by digital transformation and pioneering problem-solving approaches.
Let's grab this opportunity with both hands and drive our industry into a smarter, more efficient future.