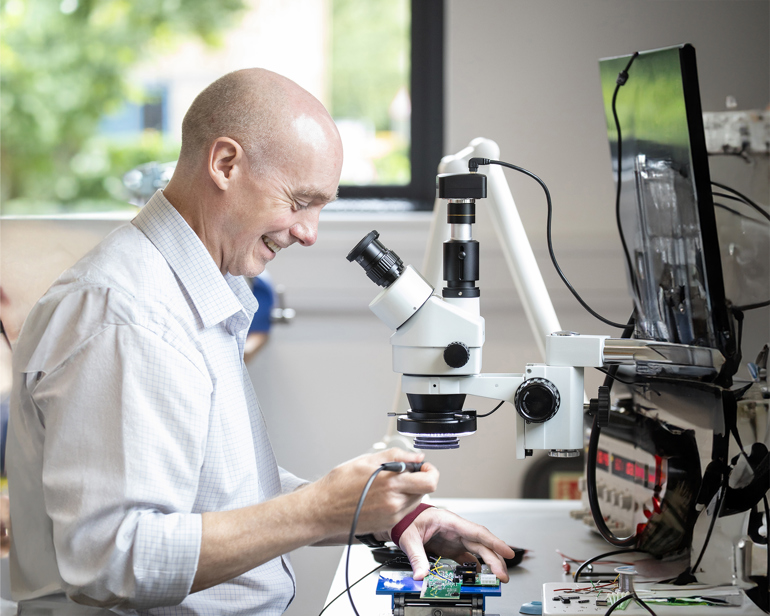
"We believe in the problem solved" – These words have driven innovation at my family’s company for four decades. The journey from identifying a problem to crafting an award-winning solution will always come with challenges and demands, but it’s worth it when you see the product making a difference.
It requires a fine balance of drawing influence from our heritage, listening intently to customers, championing safety and efficiency, and nurturing an appetite for innovation.
Above all, the journey demands the courage to “give it a go”, take risks, and be different.
Using heritage as a foundation
Innovation in manufacturing is built upon the foundations laid by the generations of industrious engineers and designers who came before us.
When my family set out to revolutionize industrial safety barriers, we scrutinized steel structures. We asked why steel had been the go-to material for so long and what underlying needs it addressed. This deeper understanding allowed us to identify areas ripe for disruption.
But while staying true to our heritage, it is important to avoid being shackled by tradition. The key is to respect the wisdom gained from our journey while having the courage to challenge it. The bold step to take a data-driven approach with our data platform CONEK™️ and product RackEye™️ required us to be brave, challenge the status quo, and prove that our innovative technology could outperform traditional methods in many ways.
The art of listening to customer needs
Every great product is built on a deep understanding of the customer. In manufacturing, this means getting our hands dirty on factory floors and warehouses and observing real-world conditions and challenges.
Throughout our design process, we have made it a priority to engage with our customers at every available level. From forklift operators to health & safety managers and business owners, each offering a unique perspective and valuable insights. But the art of listening goes beyond these conversations, it is also about reading between the lines and understanding the daily struggles of those whom our products protect.
The best designs require looking beyond the obvious. When we first proposed polymer barriers, many customers were skeptical. Steel was familiar. It was trusted. But by demonstrating how our solution addressed an unspoken need - reducing damage to vehicles and equipment, easier installation, and less frequent replacement - we were able to challenge and change opinions across the vertical markets we supply.
Safety and efficiency - Two sides of the same coin?
Safety and efficiency can often be seen as competing priorities. Our challenge has been to prove that they are complementary goals.
When approaching a design problem, we don't ask, "How can we make this safer?" or "How can we make this more efficient?" Instead, we start with, "How can we enhance efficiency in a way that also provides the highest level of safety?". It is taking this perspective that drives us.
By harnessing the unique properties of our patented advanced polymers, we created barriers that absorb impact more effectively than steel while reducing maintenance downtime and minimizing damage to vehicles and equipment.
A dual focus on safety and efficiency has helped us develop more innovative products. It has also changed opinions in our industry. We have demonstrated that investing in innovative safety solutions can drive productivity and profitability – it becomes a win-win scenario for businesses looking to protect their people, assets, and bottom line.
Problem-solving
Manufacturing is about solving real-world problems. We encourage a working culture where challenges are seen as opportunities. When we looked at traditional steel barriers, we saw a product with problems to be solved – energy absorption, maintenance issues, and installation challenges for varied locations. By stepping back and reframing the issue, we saw new possibilities.
We have learned to accept failure as an integral part of the design process. Each setback is an opportunity to take the learnings, rethink, and improve. Our journey to perfecting polymer barriers involved countless attempts at our dedicated test center. We performed tests at different impact angles and temperatures, using different polymer product mixes - before refinement led us to a perfect product.
By adopting this approach, we've been able to rapidly stress-test ideas, validate them in real-world conditions, and continuously enhance our designs based on feedback and performance data – because the job is never done.
Final thoughts
The journey of designing an award-winning product in manufacturing is rarely straightforward. It is a path stained by moments of frustration and flashes of inspiration, painstaking efforts and bold leaps of faith. For those who persist, walk the walk, and are brave enough to challenge the status quo, the rewards are immense.
Recently, our team was honored to receive prestigious recognition for one of our tech-led designs. While the award is fulfilling, what truly awakens us is the impact our first IoT solution will have on workplaces globally. It is a testament to what can be achieved when we approach design with a keen ear for customer needs and a commitment to safety and efficiency.
To aspiring innovators and designers, I offer encouragement - please stay curious, learn from the challenges, and enjoy the end result of a problem solved.